ダクト計画における要点概要を解説します
工場における計画について、以下に初期段階の留意点を列挙します。
工場内の機器配置
工場内の配管及び経路
建築構造、高さ、面積
サポート計画
集塵の場合、その対象箇所及び機器の取り合い
サイクロンの位置計画
バグフィルターの位置と大きさ
排風機の大きさと場所
(場合によっては、屋外、屋上に設置せざるをえない場合など)
排風機は騒音がありますので、職場環境の意味あいから、
特に屋内設置では間仕切りが必要になります
工事施工のやりやすさ、作業の安全等
を念頭に、概略ルートを選定します。
ダクトの部品点数、形状等についても以下にその留意点を記述します。
第一に考慮するべき要点として、対象気体、ガス等
及び集塵については捕集対象気体と工場内のいわゆる雰囲気と呼ばれる
粉塵の特性であります、
まず、関係してくるのが、ダクトの摩耗と詰まり等、
ルート選定に重要な要素でもあります。
その場合、機器から出てすぐにエルボ+水平にすると、
ほとんどの場合、詰まり堆積が起きますので、
まず垂直にできるだけ立ち上げ、エルボにはせず、
”R”と総称される、曲率半径を大きくとるなどの
暫定計画が必要です。
次に水平ダクトの流れ方向には立ち上げ、たち下げ、
を頻繁に繰り返すようないわゆる水平方向の起伏は基本的にNGとなります。
水平部は方向転換位置までは基本的にいけるところまで水平に伸ばすのが
セオリーとなっています。
とは言いましても、ケースバイケースでこのあたりも含め、
思案のしどころでもあります、
弊社、株式会社アイエヌジーヘご相談していただくことを、おすすめ致します。
状況を踏まえたなかでの計画、設計、製作、施工まで最善対応を致しております。
低圧ダクト高圧ダクト
内部風速と静圧により低速ダクトと高速ダクトに分類され
ダクト呼称と圧力範囲
(日本冷凍空調学会より)
低圧ダクト:
常用圧力(Pa) +490 -490
Kgf/? +0.005
-0.005
制限圧力(Pa) +980以下 ?735以下
Kgf/? +0.01
-0.008
流速範囲:15m/s以下
高圧1ダクト:
常用圧力(Pa)
?490を超え+980以下
?490を超え?980以下
制限圧力(Pa) +1470以下 ?1470以下
流速範囲:20m/s以下
高圧2ダクト:
常用圧力(Pa)
?980を超え+2450以下
?980を超え?1960以下
制限圧力(Pa)
+2940以下 ?2450以下
流速範囲:20m/s以下
常用圧力と制限圧力の定義:
常用圧力:通常運転の最大のダクト内の静圧
制限圧力:ダクト内のダンパの急閉などにより
一時的に圧力が上昇する場合の制限圧力
尚、高圧1ダクト高圧2ダクトを排煙用として使用する場合は、流速上限は 25m/s程度となっています。
ダクト設計
ダクト設計に於いての計画に基き、ダクト設計製作工事までの工程を踏まえた、
設計の骨子を解説します。
風速:単位はメートル毎秒で一般の台風などと単位は同じです、
風量:ダクト関係(丸、角形状)では特に立法メートル毎分です、
対応する排風機、サイクロン、バグフィルターの処理風量も同じ単位を使用します、
ダクト設計における圧力単位は、静圧という概念で行います、
単位はmmAq(ミリアクア)mmH2O(ミリ水柱)を用います。
ダクト風量計算にはダクト径はメートル単位になります。
常温域では、風量(立法メートル/分)=60x風速xダクト内径有効面積(平方メートル)となります。
排風機出口には消音器(サイレンサー)を介して大気に放出するのが一般的です。
設計上更に必要な要素として、ダクト内を流れる気体に対して、
圧力損失が発生しますので、そのパラメータとして、一ラインの区切り単位ごとに
各々直管の有効径と長さ、エルボの個数、分岐箇所とその数、径違い箇所とその数等を算定し
トータル的には合算値になります。
そして、ダクト計画がその後において影響します。
専門的には特に、ダクトの材質、板厚が重要な要素となってきますが、
通常の配管材、加工品(スパイラルダクト)など圧力、摩耗、耐久性、重量など
実務経験などが関係する専門的な範囲にはいりますのでここでは、割愛します。
弊社、株式会社アイエヌジーヘご用命していただくことを、おすすめ致します。
煙道ダクト
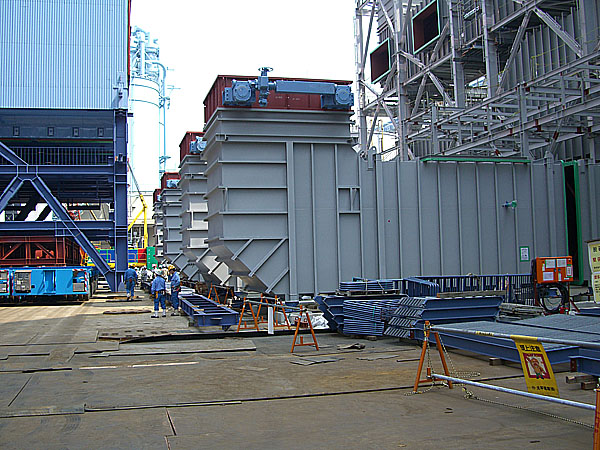
煙や燃焼排ガスを、炉またはボイラーから煙突に導く目的で設計製作されます、
比較的外形が大きいものがありますので板厚も通常のダクトより厚く溶接構造となり補強リブが入ります。
又、耐熱塗装をすることも一般的です。
集塵ダクト
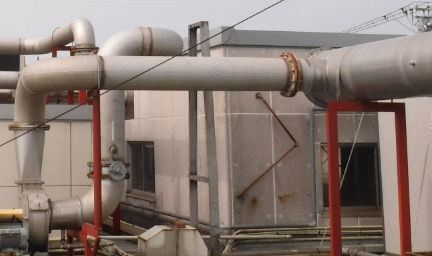
集塵ダクトの主な必要性には、
工場における局所集塵(オープンスペースから発生するもの)
特に、局所集塵については多種多様の環境から発生しますので、
その条件は多義にわたります。
機器から発生する粉塵の捕集などが挙げられます。
大まかななが流れとしましては、
捕集箇所⇒ダクトの合流⇒サイクロン⇒バグフィツター⇒排風機⇒サイレンサー⇒大気放出
が最もオーソドックスであり又一般的です。
各要素につきましては、上述のダクト計画、ダクト設計を合わせてご覧ください。
脱臭及び廃ガス処理
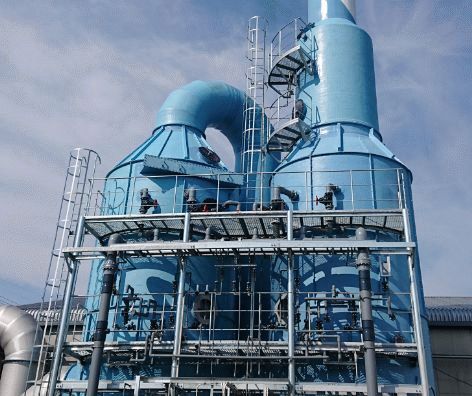
脱臭処理、ガス処理につきまして、その概要を解説致します。
脱臭処理については、その発生場所は基本的に集塵箇所ろ類似してはいますが、
捕集した後の処理工程はかなり複雑になります
構成機器はおおまかには、サイクロン、スクラバー、コンデンサ、ミストセパレーター、
脱臭フィルター、化学反応させる場合もあれば、脱臭炉で加熱処理をする場合など、多際な工程を含みます。
匂いの成分、構成要素等化学的知見のもとに行われます。
更に臭気レベルごとに専門ラインも組まれます。
計画の骨子として、ほとんどの場合、臭気の問題性など傾向として大径ダクトになりがちです。
廃ガス処理は共通点としてダクトがつかわれますが、その科学性、温度など
専門性が強い分野になりますので、プロセス等含めますと多種多様な化学分野が含まれます、
遮断回路も含まれ、更には配管設計、バルブ類も含まれます。
排ガスダクト相互の処理工程をつなぐ連絡路的な要素が色濃く出る分野でもあります。
ダクト施工
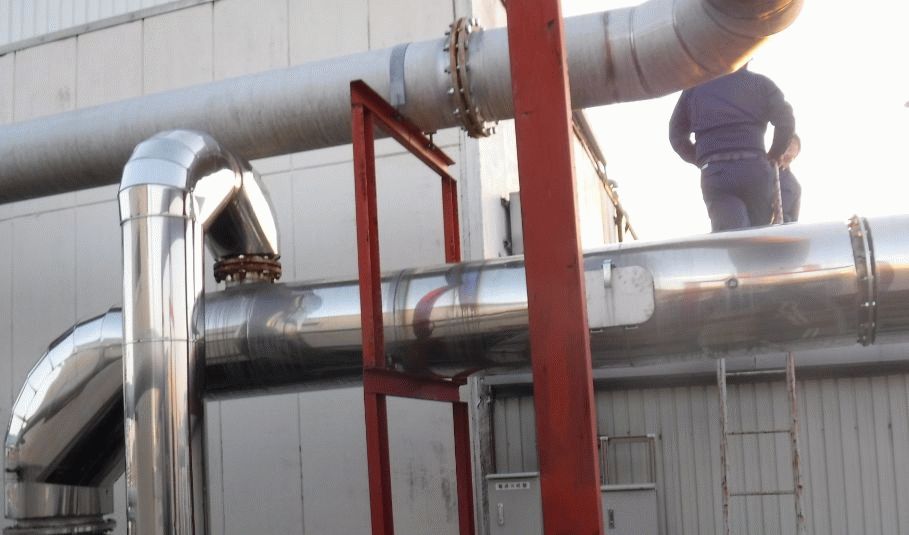
ダクト施工はダクト設計製作据え付け工事と連なる、最終工程であります。
その特徴を以下に解説します、
ダクトに配管材を使用した場合:
接続部は、フランジ+ガスケットあるいはヤーンロープなどでシールをします。
配管そのものの製品化には専門性の強い溶接技術も問われます、
又そのフランジ箇所を考慮して更にピッチ間隔なども重要になりサポート位置がきまります、
一般的には、各種形鋼材が使われ、
このサポート方法には従来より多種多様な方法が考案され、
会社、業者により基準が設けられることも一般的になっています、
又、その支柱である架台に及んでは、機械構造力学、機械設計の知識も必須になってきます。
最も、この部分については、設計段階で製作図面化になりますが、
スパイラルダクトのように、薄鋼板を利用したスパイラル加工された製品も使います、
但し、留意する点も多く、施工には、それなりの施工技術が必須とされます、
ダクトのつなぎ方法には、接続のためのスリーブ、ビスネジ、テープ、などを使います、
接続部品が非常に多く、その知識経験が必要になり、サポートの種類まで入れると、
複雑な手順になります、
又、強度的にも細心の注意がもとめられますが、軽量化というメリットがあります。
使用圧力に制限があり、その使用に関してメーカーが注意喚起している分野でもあります。